Automotive lighting leak testing is a crucial process in the automotive industry to ensure the safety and functionality of vehicle lighting systems. Leak testing is performed to detect any potential leaks in the lighting components, such as headlights, taillights, turn signals, and other lighting fixtures. By identifying and fixing leaks, manufacturers can prevent water or moisture ingress, which can lead to electrical failures, malfunctions, corrosion, reduced visibility, and potential safety hazards.
Leak Testing Methods
There are several leak test methods used in automotive lighting manufacturing, each with its own advantages and limitations. These methods include Water Immersion, Pressure or Vacuum Decay, Mass Flow and Metered Volume. Trace gas leak testing wasn’t considered due to its excessive cost.
Water Immersion Test
This method involves immersing the lighting component in water and applying pressure to simulate real-world conditions. Any leaks or water ingress are detected by visible bubbles during pressurization. Water immersion is the least expensive method. However, this method is time consuming, highly subjective, creates safety concerns and (due to moisture) not suitable for all types of lighting fixtures or manufacturing environments.
Pressure or Vacuum Decay Test
This method is used to detect leaks in the 1-1000 sccm leak rate range. With this type of test, a specific pressure or vacuum is applied to the lamp, After stabilizing, the tester measures the decay rate to determine product acceptance. During initial setup, the decay characteristics of a “Master” non-leaking lighting component with and without a known leak rate are memorized. Production components are then referenced to these characteristics to verify the component passes the leak criteria. Decay testing is simple & inexpensive with good resolution. The smaller the pressure detected the slower the test. Decay testing is also volume dependent. If the lamp volume is variable (excessive stretching under pressurization) the test results will be variable as well.
Mass Flow Test
This method is used to detect leaks in the 1sccm to – 100LPM leak rate range. Like Pressure Decay, with a Mass Flow the part is pressurized and allowed to stabilize. Once stabile, the leak tester measures the amount of “replacement” air volume needed to maintain the setpoint pressure. Any replacement air required to maintain the setpoint is considered leakage and based on the leak limits applied, the part is passed or rejected. Mass flow testing is simple & inexpensive with excellent resolution. It’s the preferred test method for lamps that are plastic/elastic (stretch and grow) when pressurized. Also lamps that may vary in volume or have large dead volumes.
Metered Volume Test
This technique is used for sealed lamps. Essentially lamps without a port or hole to pressurize or pull a vacuum. For this method, the test lamp is placed into a chamber that’s closely knitted to the contours of the part. Once the chamber is sealed, the leak tester delivers a known volume of air at known pressure into the chamber. If the lamp is leaking, the chamber pressure will start to degrade, indicating a leak. Metered Volume testing is simple & with good resolution. Skill is required to produce the correct chamber for the application. Testing is also needed to ensure the process can detect a gross leak condition prior to filling the part to pressure.
Cutting-Edge Technology
LeakMaster works with the world’s largest Automotive Lighting manufacturers to provide leading-edge technology, such as our UltraFlow V3 and Defender leak testers.
ULTRAFLOW V3
The ULTRAFLOW V3 leak tester is specifically designed to test automotive lamps and configured to test with either pressure decay or mass flow. Occlusion testing is available as well, to check for blocked or flashed openings. The UltraFlow utilizes our patented pneumatic design which allows the instrument to test lamps at a faster rate, while eliminating the “false rejects” associated with other leak tester brands.
ULTRAFLOW V3-RT
The ULTRAFLOW V3-RT (Remote Touchscreen) is perfect for smaller workstations with limited space. With this configuration, the HMI can be mounted in a user-friendly location for programming and visual pass/fail status while the instrumentation enclosure can be tucked in a convenient location.
DEFENDER
The DEFENDER lamp tester is considered the best value of any pressure or vacuum decay leak tester on the market and can perform a metered volume test as well. Compact yet powerful, while providing excellent value and return on investment describe the Defender. It’s built for production usage and with Ethernet IP onboard, ready for seamless integration with Allen Bradley devices.
Automotive Lighting Leak Testing
Why should you leak test lighting systems?
Safety
Properly functioning lighting systems are crucial for driver visibility and safety. Leaks can compromise their performance, leading to reduced visibility and potential accidents.
Durability
Water or moisture ingress can cause electrical failures & corrosion. By identifying and fixing leaks, manufacturers ensure the durability and longevity of their products.
Regulatory compliance
Automotive lighting systems must meet various regulatory standards and requirements. Leak testing helps manufacturers ensure that their products are safe and legal for use on the roads.
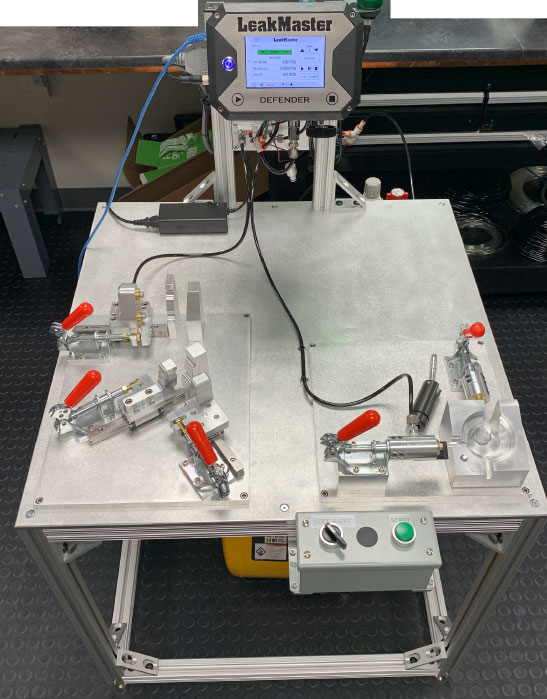
Contact Us Today
Want more information? Contact us for details regarding our lighting leak testers or other products or services.